Produce Hydrogen Efficiently & Cost-effectively Through An All-3D-Printed Electrolyzer
From:
Zhonglin International Group Date:03-12 1125 Belong to:Industry Related
Recently, a team of from Northwestern Polytechnical University, led by academician Huang Wei and professor Guan Cao, developed an all-3D-printed electrolyzer based on a high-precision three-dimensional nickel metal structure.
Driven by solar panels, this electrolyzer is capable of stable and efficient water decomposition, allowing a voltage of 1.63V to drive a current density of 500mAcm-2, and can operate stably for over 1000 hours without significant performance degradation.
When assembled with commercial solar panels, this device works well and can truly promote environmental-friendly energy development, helping to meet the growing energy needs of human society.
In addition, the device has good high activity and durability, providing a feasible method for the large-scale and customized production of renewable energy.
Its potential applications mainly include the following two directions:
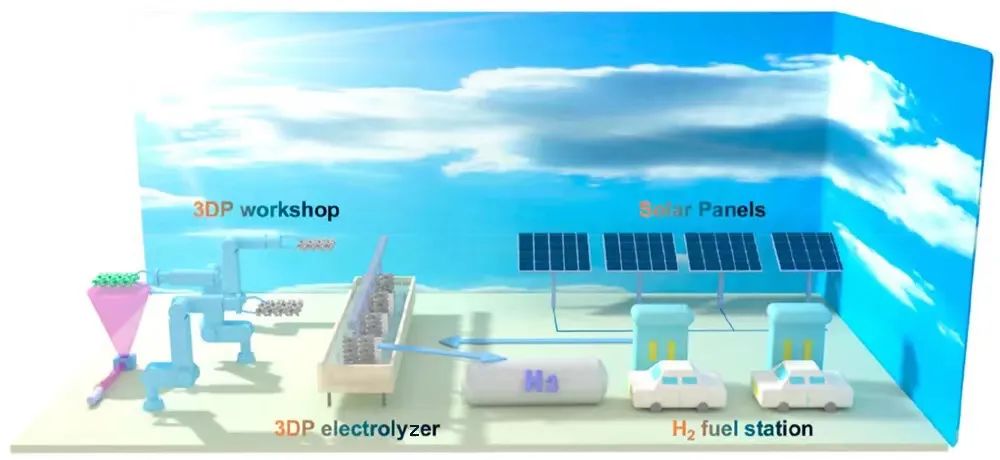
Firstly, it is used for electrolysis of water to produce hydrogen. The 3D printed electrode designed this time can not only be used for electrolysis of water in alkaline environments at industrial level current density, but also be further extended to the field of electrolysis of water in seawater environments, providing new solutions for sustainable hydrogen production processes.
Secondly, for battery energy storage. This fully 3D printed electrode has a unique three-dimensional structure, which combines high energy density, good rate capability, and excellent durability. Therefore, it can also be used in metal air batteries and nickel hydrogen batteries.
In this study, transition metal-based materials of MoNi4 and NiFe LDH were prepared by the reduction site of the research group through photo curing precursor method, which were used as electrocatalysts for hydrogen evolution reaction and oxygen evolution reaction, respectively.
By increasing the specific surface area of the electrode structure, the active sites of the electrode can be increased and the loading of active substances can be increased, thereby further improving the catalytic efficiency of water electrolysis. It can be seen that using a three-dimensional structure as the electrode structure is the most effective method to increase the specific surface area.
However, based on industrial level current density, water decomposition also faces another problem: the problem of bubble adhesion under high current.
A high current density means that more bubbles are generated. When bubbles adhere to the surface, the active sites are covered, making it impossible to participate in catalytic reactions and reducing catalytic efficiency.
This indicates that simply improving materials and increasing specific surface area cannot truly achieve efficient and stable water decomposition. So, it is necessary to achieve efficient and stable water decomposition through the synergistic effect between structural design and material control.
To further improve the electrocatalytic performance and stability, and ensure that the electrode structure has a sufficiently large electrochemical active area, the research group adopts a 3D printed hierarchical ordered porous three-dimensional structure to improve the bubble escape behavior under high current density.
After the formation of bubbles, this hierarchical ordered porous structure can quickly escape from the inside of the structure, avoiding the formation of blockage and aggregation on the electrode surface, making the electrode active sites close to their inherent active sites under high current density. This approach can not only improve mass transfer efficiency, but also reduce the additional overpotential generated during the transmission process.
Under the synergistic effect of structure and materials, the overpotentials of the composite electrode at a current density of 500mAcm-2 in hydrogen evolution reaction and oxygen evolution reaction are 104mV and 310mV, respectively, which are superior to many electrode materials previously reported in academia.
It is reported that in recent years, although precious metal-based catalysts have shown excellent catalytic performance in electrolytic water, these precious metal catalysts have the disadvantages of high cost and poor stability, resulting in high cost of electrolytic water and limiting its application in actual industrial hydrogen production.
In addition to precious metal catalysts, transition metal nickel-based catalysts also exhibit great potential in alkaline electrolysis of water. Compared with precious metal catalysts, transition metal nickel-based catalysts not only have lower costs but also better stability.
Although the catalytic efficiency of transition metal nickel-based catalysts is not as good as that of precious metals, by improving the structure and optimizing the material composition, the catalytic efficiency can be effectively improved.
The above is the background of this study. More specifically, this work originated from an experimental phenomenon discovered by the research group a year ago.
At that time, they found that when the most commonly used foam nickel was used as the electrode substrate to load the active material, then the electrolytic water performance test was carried out. When the current density was about 10mAcm-2, the linear scanning voltammetry curve was very smooth; When the current density increases by several tens of times to around 500mAcm-2, the linear sweep voltammetry curve exhibits drastic fluctuations.
By observing the experimental phenomena inside the electrolysis tank during the process of electrolyzing water, the team found that after a high current was applied to the electrode surface, the number of bubbles increased sharply, and some large bubbles adhered to the electrode surface for a long time before disappearing from the electrode surface in the form of rupture.
During the process, the linear sweep voltammetry curve showed serrated fluctuations, so they speculated that the influence of bubble behavior on catalytic performance may also play a crucial role.
When using the photo curing method of the research group to print the metal electrode structure, this phenomenon was significantly improved, which means that the structure also affects the behavior of bubbles.
To verify this idea, they utilized 3D printing technology of digital light processing to design and prepare a three-dimensional hierarchical ordered porous Gyroid structure. Then, the team took this as the electrode structure and compared it with the commercial foam nickel three-dimensional framework structure to explore the impact of different structures on bubble behavior and catalytic performance.
Based on the exploration of 3D printing technology by the research group, the electrode preparation in the early stage went very smoothly. However, it takes relatively longer to demonstrate the influence of structure on bubble behavior through experiments.
In the experiment of studying bubble behavior, they initially only proposed the conjecture that structural design would affect catalytic performance, and did not develop a detailed experimental plan.
After reading literature and summarizing, the experimental method was finally finalized. During this period, they gradually explored, including building specialized experimental equipment and learning shooting methods for subsequent paper writing.
Finally, through a series of experiments, the team proved its original idea that the escape time of bubbles in 3D printed hierarchical porous structure is significantly shorter than that in foam nickel.
Moreover, no adhesion of large bubbles was observed in the 3D printed electrodes. This indicates that the movement of bubbles is obviously affected by the disordered pore structure of foam nickel, and takes precedence over the in-plane movement rather than the out of plane movement.
Different from foam nickel, the 3D printing electrode has a hierarchical and orderly porous structure, which allows the bubbles to escape quickly during the rising process, so it has smaller bubble size and shorter bubble escape time.
Specifically, in the catalytic performance testing of electrolyzed water, the 3D printed electrode also exhibited superior catalytic performance and a smoother linear sweep voltammetry curve.
Subsequently, the team conducted comparative tests on the stability of the single electrode. The results showed that compared with the composite electrode of foam nickel, the 3D printed composite electrode showed less voltage fluctuation in the 25-hour stability test, whether under low current density or high current density.
Afterwards, they used the modeling software COMSOL to simulate the effects of different bubble numbers and sizes on the electrolyte potential, further confirming the previously proposed viewpoint that the presence of large bubbles would cause significant disturbance to the potential, thereby affecting catalytic efficiency.
At the same time, they also considered another issue, which is that when conducting water electrolysis reactions in the same electrolysis cell, the hydrogen and oxygen produced will mix up in the electrolysis cell.
For actual production, on the one hand, this will reduce the purity of hydrogen, and on the other hand, there is also a risk of explosion caused by the mixing of hydrogen and oxygen. Therefore, the research group designed and printed a diaphragm to prevent gas mixing, which can only pass ions and not gas molecules.
In alkaline environments, hydroxide ions can freely pass through the membrane without interference, and the resulting hydrogen and oxygen cannot pass through the membrane.
In addition, in order to further achieve low-cost and efficient electrolysis of water, the team prepared the electrolysis tank mentioned earlier using 3D printing technology, and assembled it with 3D printed composite electrodes and membranes to form a fully 3D printed electrolysis water device.
Finally, the relevant paper was titled "High Efficiency All-3D Printed Electrolyzer Tours Ultra table Water Electrolysis" and published in Nano Letters. Associate Professor Xu Qian from Northwestern Polytechnical University serves as the first author, while Academician Huang Wei and Professor Guan Cao serve as co corresponding authors.
In the future, they plan to conduct further research from two aspects: material composition control and structural design in 3D printing.
In terms of material composition control, currently 3D printing is used for single metal electrodes, and based on the advantages of 3D printing, alloy electrodes can be attempted to achieve efficient catalytic and corrosion resistance performance through the synergistic effect between metals, thereby further achieving the preparation of efficient and stable electrodes in seawater environments.
In terms of structural design, the Gyroid structure has shown sufficiently excellent performance in bubble reactions, so the advantage of the Gyroid structure in bubble escape can be further strengthened through gradient structures. In addition, in addition to this structure, new three-dimensional electrode structures can also be designed by improving fluid dynamics and specific surface area.
Driven by solar panels, this electrolyzer is capable of stable and efficient water decomposition, allowing a voltage of 1.63V to drive a current density of 500mAcm-2, and can operate stably for over 1000 hours without significant performance degradation.
When assembled with commercial solar panels, this device works well and can truly promote environmental-friendly energy development, helping to meet the growing energy needs of human society.
In addition, the device has good high activity and durability, providing a feasible method for the large-scale and customized production of renewable energy.
Its potential applications mainly include the following two directions:
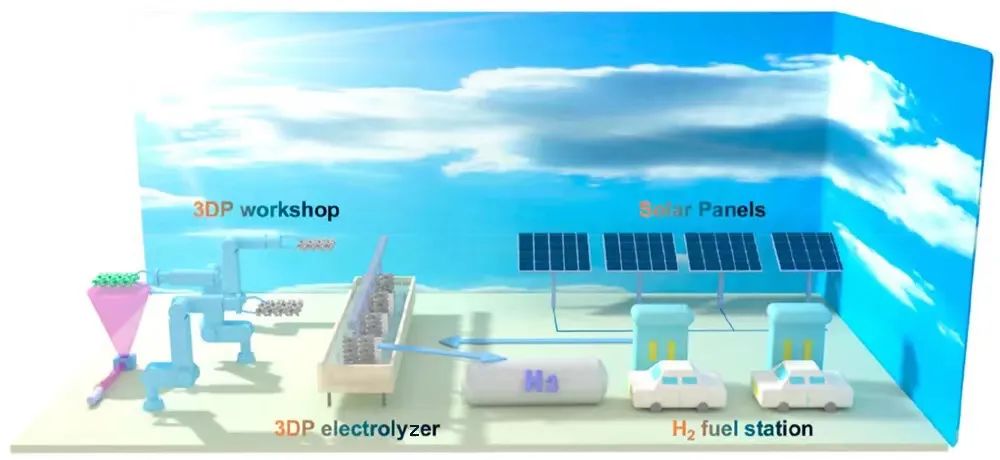
Firstly, it is used for electrolysis of water to produce hydrogen. The 3D printed electrode designed this time can not only be used for electrolysis of water in alkaline environments at industrial level current density, but also be further extended to the field of electrolysis of water in seawater environments, providing new solutions for sustainable hydrogen production processes.
Secondly, for battery energy storage. This fully 3D printed electrode has a unique three-dimensional structure, which combines high energy density, good rate capability, and excellent durability. Therefore, it can also be used in metal air batteries and nickel hydrogen batteries.
In this study, transition metal-based materials of MoNi4 and NiFe LDH were prepared by the reduction site of the research group through photo curing precursor method, which were used as electrocatalysts for hydrogen evolution reaction and oxygen evolution reaction, respectively.
By increasing the specific surface area of the electrode structure, the active sites of the electrode can be increased and the loading of active substances can be increased, thereby further improving the catalytic efficiency of water electrolysis. It can be seen that using a three-dimensional structure as the electrode structure is the most effective method to increase the specific surface area.
However, based on industrial level current density, water decomposition also faces another problem: the problem of bubble adhesion under high current.
A high current density means that more bubbles are generated. When bubbles adhere to the surface, the active sites are covered, making it impossible to participate in catalytic reactions and reducing catalytic efficiency.
This indicates that simply improving materials and increasing specific surface area cannot truly achieve efficient and stable water decomposition. So, it is necessary to achieve efficient and stable water decomposition through the synergistic effect between structural design and material control.
To further improve the electrocatalytic performance and stability, and ensure that the electrode structure has a sufficiently large electrochemical active area, the research group adopts a 3D printed hierarchical ordered porous three-dimensional structure to improve the bubble escape behavior under high current density.
After the formation of bubbles, this hierarchical ordered porous structure can quickly escape from the inside of the structure, avoiding the formation of blockage and aggregation on the electrode surface, making the electrode active sites close to their inherent active sites under high current density. This approach can not only improve mass transfer efficiency, but also reduce the additional overpotential generated during the transmission process.
Under the synergistic effect of structure and materials, the overpotentials of the composite electrode at a current density of 500mAcm-2 in hydrogen evolution reaction and oxygen evolution reaction are 104mV and 310mV, respectively, which are superior to many electrode materials previously reported in academia.
It is reported that in recent years, although precious metal-based catalysts have shown excellent catalytic performance in electrolytic water, these precious metal catalysts have the disadvantages of high cost and poor stability, resulting in high cost of electrolytic water and limiting its application in actual industrial hydrogen production.
In addition to precious metal catalysts, transition metal nickel-based catalysts also exhibit great potential in alkaline electrolysis of water. Compared with precious metal catalysts, transition metal nickel-based catalysts not only have lower costs but also better stability.
Although the catalytic efficiency of transition metal nickel-based catalysts is not as good as that of precious metals, by improving the structure and optimizing the material composition, the catalytic efficiency can be effectively improved.
The above is the background of this study. More specifically, this work originated from an experimental phenomenon discovered by the research group a year ago.
At that time, they found that when the most commonly used foam nickel was used as the electrode substrate to load the active material, then the electrolytic water performance test was carried out. When the current density was about 10mAcm-2, the linear scanning voltammetry curve was very smooth; When the current density increases by several tens of times to around 500mAcm-2, the linear sweep voltammetry curve exhibits drastic fluctuations.
By observing the experimental phenomena inside the electrolysis tank during the process of electrolyzing water, the team found that after a high current was applied to the electrode surface, the number of bubbles increased sharply, and some large bubbles adhered to the electrode surface for a long time before disappearing from the electrode surface in the form of rupture.
During the process, the linear sweep voltammetry curve showed serrated fluctuations, so they speculated that the influence of bubble behavior on catalytic performance may also play a crucial role.
When using the photo curing method of the research group to print the metal electrode structure, this phenomenon was significantly improved, which means that the structure also affects the behavior of bubbles.
To verify this idea, they utilized 3D printing technology of digital light processing to design and prepare a three-dimensional hierarchical ordered porous Gyroid structure. Then, the team took this as the electrode structure and compared it with the commercial foam nickel three-dimensional framework structure to explore the impact of different structures on bubble behavior and catalytic performance.
Based on the exploration of 3D printing technology by the research group, the electrode preparation in the early stage went very smoothly. However, it takes relatively longer to demonstrate the influence of structure on bubble behavior through experiments.
In the experiment of studying bubble behavior, they initially only proposed the conjecture that structural design would affect catalytic performance, and did not develop a detailed experimental plan.
After reading literature and summarizing, the experimental method was finally finalized. During this period, they gradually explored, including building specialized experimental equipment and learning shooting methods for subsequent paper writing.
Finally, through a series of experiments, the team proved its original idea that the escape time of bubbles in 3D printed hierarchical porous structure is significantly shorter than that in foam nickel.
Moreover, no adhesion of large bubbles was observed in the 3D printed electrodes. This indicates that the movement of bubbles is obviously affected by the disordered pore structure of foam nickel, and takes precedence over the in-plane movement rather than the out of plane movement.
Different from foam nickel, the 3D printing electrode has a hierarchical and orderly porous structure, which allows the bubbles to escape quickly during the rising process, so it has smaller bubble size and shorter bubble escape time.
Specifically, in the catalytic performance testing of electrolyzed water, the 3D printed electrode also exhibited superior catalytic performance and a smoother linear sweep voltammetry curve.
Subsequently, the team conducted comparative tests on the stability of the single electrode. The results showed that compared with the composite electrode of foam nickel, the 3D printed composite electrode showed less voltage fluctuation in the 25-hour stability test, whether under low current density or high current density.
Afterwards, they used the modeling software COMSOL to simulate the effects of different bubble numbers and sizes on the electrolyte potential, further confirming the previously proposed viewpoint that the presence of large bubbles would cause significant disturbance to the potential, thereby affecting catalytic efficiency.
At the same time, they also considered another issue, which is that when conducting water electrolysis reactions in the same electrolysis cell, the hydrogen and oxygen produced will mix up in the electrolysis cell.
For actual production, on the one hand, this will reduce the purity of hydrogen, and on the other hand, there is also a risk of explosion caused by the mixing of hydrogen and oxygen. Therefore, the research group designed and printed a diaphragm to prevent gas mixing, which can only pass ions and not gas molecules.
In alkaline environments, hydroxide ions can freely pass through the membrane without interference, and the resulting hydrogen and oxygen cannot pass through the membrane.
In addition, in order to further achieve low-cost and efficient electrolysis of water, the team prepared the electrolysis tank mentioned earlier using 3D printing technology, and assembled it with 3D printed composite electrodes and membranes to form a fully 3D printed electrolysis water device.
Finally, the relevant paper was titled "High Efficiency All-3D Printed Electrolyzer Tours Ultra table Water Electrolysis" and published in Nano Letters. Associate Professor Xu Qian from Northwestern Polytechnical University serves as the first author, while Academician Huang Wei and Professor Guan Cao serve as co corresponding authors.
In the future, they plan to conduct further research from two aspects: material composition control and structural design in 3D printing.
In terms of material composition control, currently 3D printing is used for single metal electrodes, and based on the advantages of 3D printing, alloy electrodes can be attempted to achieve efficient catalytic and corrosion resistance performance through the synergistic effect between metals, thereby further achieving the preparation of efficient and stable electrodes in seawater environments.
In terms of structural design, the Gyroid structure has shown sufficiently excellent performance in bubble reactions, so the advantage of the Gyroid structure in bubble escape can be further strengthened through gradient structures. In addition, in addition to this structure, new three-dimensional electrode structures can also be designed by improving fluid dynamics and specific surface area.