China's Solution to Produce Green Aviation Fuel Through Carbon Dioxide
From:
Zhonglin International Group Date:03-22 1425 Belong to:Industry Related
With the development of non aqueous renewable energy sources such as photovoltaics and wind energy, as well as electrochemical energy storage, the electrification of transportation vehicles has become the main technological route for reducing CO2 emissions in the transportation sector. However, in response to the rapidly developing aviation industry, the huge gap between the energy density of commercial lithium-ion batteries (0.54-1.26 MJ/kg) and aviation fuel (34.9-40.6 MJ/L) makes it difficult to achieve rapid electrification in the foreseeable future aviation industry, and there is an urgent need for a feasible technology to achieve the "carbon neutrality" goal of the aviation industry.
Green aviation fuel refers to C8-15 liquid hydrocarbon fuels derived from non fossil resources. According to the lifecycle analysis of Global Oil Company in the United States, the greenhouse gas emissions of green aviation fuel are reduced by 65% to 85% compared to petroleum based aviation fuel. During use, it exhibits a higher energy density, allowing the aircraft to fly further while consuming less fuel. All key indicators of aviation fuel, such as flash point, freezing point, stability, and combustion heat, meet or even exceed existing aviation fuel standards and specifications. When existing aircraft switch to bio aviation fuel, there is no need to change the aircraft engine and fuel infrastructure, and it can be used directly and conveniently. In this case, green aviation fuel is recognized as a feasible path to reduce carbon dioxide emissions in the world aviation transportation industry.
As of the end of 2020, airlines in more than ten countries around the world have been testing biofuels, and a total of 65 countries have implemented mandatory blending instructions for green aviation fuel. The Renewable Energy Directive of the European Union (EU) requires that the proportion of green aviation fuel added should not be less than 5% by 2030 and 63% by 2050. In 2019, global aviation fuel consumption reached 360 million tons, indicating that the current global production and sales of green aviation fuel are only one thousandth of the total aviation fuel consumption, and there is huge potential for future growth.
At present, green aviation oil is mainly obtained from the cracking and refining of bio fats, with low yield and high energy consumption. Its selling price is as high as 2700-3100 US dollars/ton, which is four times that of petroleum based aviation coal. The high price limits its promotion and application, and how to selectively obtain green and low-cost aviation fuel has become an academic hotspot and industry pain point.
Last year, the research team of the Department of Chemical Engineering at Tsinghua University successively published research results in ACS Catalysis and Nature Communications, marking significant progress in the field of CO2 to Aviation Fuel (CO2AFTM) production by the research team.
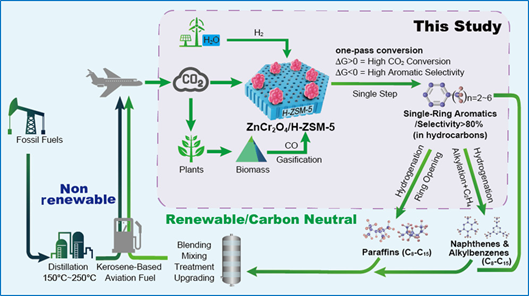
01 Technical introduction
The research team at Tsinghua University has designed a process route targeting aromatic aviation coal fractions (C8-C15) as the target product, achieving a spontaneous reaction pathway for CO2 hydrogenation thermodynamically; Developing a self initiated monodisperse metal strategy on metal oxide molecular sieve acid-base heterojunctions, while maintaining over 80% of the directed conversion of aromatic hydrocarbons, increases the CO ₂ hydrogenation ability by three times. At the same time, the gas-solid structure characteristics inside the high-pressure hydrogenation multiphase flow reactor were explored to meet the strict requirements for temperature and concentration field uniformity in the CO ₂ hydrogenation process, laying a solid foundation for the conceptualization and industrialization of CO ₂ hydrogenation to produce green aviation fuels and chemicals.
The "green" of technology is reflected in the entire process. There are two raw material pathways: one is to use biomass as raw material, and synthesize bio aviation kerosene through one-step synthesis of carbon monoxide, carbon dioxide, and hydrogen obtained from biomass gasification; Another method is to use captured carbon dioxide as raw material and synthesize green aviation kerosene through carbon dioxide hydrogenation. The former fully utilizes renewable carbon resources in biomass by supplementing a certain amount of green hydrogen (or blue hydrogen) externally; The latter can flexibly plan the project scale based on the amount of green hydrogen resources obtained and the cost of green hydrogen.
02 Technical advantages
There are two existing production paths for bio aviation kerosene:
Firstly, the hydrogenation refining method that obtains bio aviation kerosene by hydrogenation refining vegetable oil, gutter oil, or other high oil substances. This type of aviation kerosene has a similar carbon number distribution to conventional petroleum based aviation kerosene. Representative technologies include the next-generation renewable jet fuel technology of NESTEOIL in Finland and the renewable aviation fuel process of Honeywell UOP in the United States. The advantages of the hydrogenation refining method are mainly reflected in its mature technology, flexible product adjustment (which can flexibly adjust the production of green aviation kerosene and green diesel according to market demand), and strong adaptability to the market. However, the limitation of raw material sources (various oils and fats, seaweed, and shepherd's purse) is the biggest problem of the hydrogenation refining method, especially the competition between vegetable oil raw materials and humans for food and land. The other main source, gutter oil, has been continuously rising in price due to its scattered distribution, poor procurement channels, and insufficient supply. Currently, it has reached 6000-7000 yuan/ton, which has increased the cost of the final product, bio aviation kerosene, and also affected the widespread promotion and application of this technology.
Secondly, the Fischer Tropsch synthesis method that uses biomass such as cellulose and lignin as raw materials, first gasifies to generate syngas, which is then used to synthesize wax. The wax is then hydrocracked and hydroisomerized to produce bio aviation kerosene. Representative technologies include the first generation of bio aviation fuel and renewable diesel technology developed by Nesteoil in Finland, the iron-based catalytic high-temperature Fischer Tropsch synthesis process developed by Sasol in South Africa, and the inverse transformation+Fischer Tropsch synthesis process launched by Johnson Matthey in January 2022. The Fischer Tropsch synthesis method has a wide range of raw materials and significant carbon reduction effects, but the main components of the obtained liquid fuel are straight chain alkanes from C2 to C90. The C8 to C15 components that can truly be used as high-quality aviation kerosene only account for 25% of the synthesized product, and there are no cycloalkanes and aromatics, resulting in a low specific gravity and energy density of the obtained aviation kerosene, which means that the flight range of aircraft carrying the same volume of Fischer Tropsch synthesis fuel oil is short.
Compared to the above technologies, the entire process path of CO2AFTM technology at Tsinghua University is green. Specifically, there are four advantages: firstly, the obtained aviation kerosene components are concentrated in C9 to C11 aromatics, and the selectivity of high-quality aviation kerosene components exceeds 80%. By blending with straight chain alkanes, qualified aviation kerosene products can be obtained. Secondly, the selection of aromatic rings as the final product improved the thermodynamic efficiency of the reaction process, resulting in high energy utilization efficiency and significant energy-saving effects. Thirdly, by using acid-base heterojunction catalysts, the reaction can be carried out under mild conditions of 270~370 ℃ and above 2MPa, with lower overall energy consumption and cost. The fourth is that the source of raw materials is extensive and sustainable - this technology can produce synthetic gas from renewable energy sources such as biomass, and then produce aviation kerosene in a one-step process. It can also capture and purify carbon dioxide emissions from industrial enterprises, and produce aviation kerosene in a one-step process with hydrogen gas, thereby achieving dual carbon reduction and resource utilization. It is a truly green, low-carbon, and even negative carbon aviation kerosene production process.
03 Progress
A 100 ton/year trial has been completed, verifying the selectivity, stability, effectiveness, and safety of the catalyst, demonstrating the scientific, rational, and feasible nature of the entire process flow. From the results of the small-scale trial, it can be seen that the carbon dioxide hydrogenation technology for one-step production of green aviation kerosene consumes approximately 3.3 tons of carbon dioxide, 0.43 tons of hydrogen, and 0.5kg of catalyst for every 1 ton of aviation kerosene produced. Moreover, the catalyst has not significantly deactivated after continuous use for 3000 hours.
At present, the 10000 ton industrial testing device constructed using this technology is under construction and is expected to be put into trial operation in 2023. This industrial experimental device will mainly solve some problems that cannot be detected in small-scale tests during the engineering process of catalysts and process, but may affect the long-term operation of future industrial demonstration devices. After the industrial experiment is completed, a process package of 100000 to million tons can be formed based on the scale of green hydrogen, and industrial promotion and application can begin steadily.
The total investment for constructing a 300000 ton/year device using this technology is approximately 4.5 billion yuan. If using photovoltaic technology to produce green hydrogen, a 4.5Gw photovoltaic system (calculated at 1600 hours/year for photovoltaic power generation) and 180 sets of 1000 cubic meters/hour electrolytic water hydrogen production equipment are required.
04 Conclusion
This technology (CO2AFTM) uses CO2 and green hydrogen as raw materials and competes with world technology giants in the field (Green Jet FuelTM from Honeywell UOP in the United States and HyCOgenTM from Johnson Matthews in Europe). It proposes a Chinese solution in the world's low-carbon core technology field, which can fix carbon, create negative carbon emissions, help achieve net zero emissions in aviation flight, and convert wind and solar new energy electricity into liquid energy, contributing to China's carbon peak by 2030 The achievement of the carbon neutrality target by 2060 is of great significance.
Green aviation fuel refers to C8-15 liquid hydrocarbon fuels derived from non fossil resources. According to the lifecycle analysis of Global Oil Company in the United States, the greenhouse gas emissions of green aviation fuel are reduced by 65% to 85% compared to petroleum based aviation fuel. During use, it exhibits a higher energy density, allowing the aircraft to fly further while consuming less fuel. All key indicators of aviation fuel, such as flash point, freezing point, stability, and combustion heat, meet or even exceed existing aviation fuel standards and specifications. When existing aircraft switch to bio aviation fuel, there is no need to change the aircraft engine and fuel infrastructure, and it can be used directly and conveniently. In this case, green aviation fuel is recognized as a feasible path to reduce carbon dioxide emissions in the world aviation transportation industry.
As of the end of 2020, airlines in more than ten countries around the world have been testing biofuels, and a total of 65 countries have implemented mandatory blending instructions for green aviation fuel. The Renewable Energy Directive of the European Union (EU) requires that the proportion of green aviation fuel added should not be less than 5% by 2030 and 63% by 2050. In 2019, global aviation fuel consumption reached 360 million tons, indicating that the current global production and sales of green aviation fuel are only one thousandth of the total aviation fuel consumption, and there is huge potential for future growth.
At present, green aviation oil is mainly obtained from the cracking and refining of bio fats, with low yield and high energy consumption. Its selling price is as high as 2700-3100 US dollars/ton, which is four times that of petroleum based aviation coal. The high price limits its promotion and application, and how to selectively obtain green and low-cost aviation fuel has become an academic hotspot and industry pain point.
Last year, the research team of the Department of Chemical Engineering at Tsinghua University successively published research results in ACS Catalysis and Nature Communications, marking significant progress in the field of CO2 to Aviation Fuel (CO2AFTM) production by the research team.
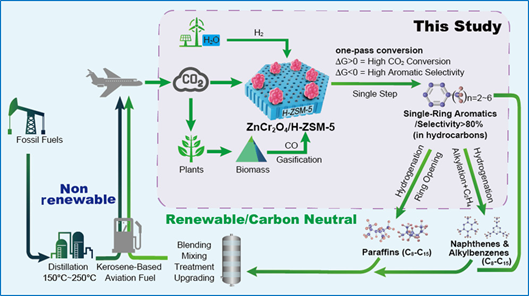
01 Technical introduction
The research team at Tsinghua University has designed a process route targeting aromatic aviation coal fractions (C8-C15) as the target product, achieving a spontaneous reaction pathway for CO2 hydrogenation thermodynamically; Developing a self initiated monodisperse metal strategy on metal oxide molecular sieve acid-base heterojunctions, while maintaining over 80% of the directed conversion of aromatic hydrocarbons, increases the CO ₂ hydrogenation ability by three times. At the same time, the gas-solid structure characteristics inside the high-pressure hydrogenation multiphase flow reactor were explored to meet the strict requirements for temperature and concentration field uniformity in the CO ₂ hydrogenation process, laying a solid foundation for the conceptualization and industrialization of CO ₂ hydrogenation to produce green aviation fuels and chemicals.
The "green" of technology is reflected in the entire process. There are two raw material pathways: one is to use biomass as raw material, and synthesize bio aviation kerosene through one-step synthesis of carbon monoxide, carbon dioxide, and hydrogen obtained from biomass gasification; Another method is to use captured carbon dioxide as raw material and synthesize green aviation kerosene through carbon dioxide hydrogenation. The former fully utilizes renewable carbon resources in biomass by supplementing a certain amount of green hydrogen (or blue hydrogen) externally; The latter can flexibly plan the project scale based on the amount of green hydrogen resources obtained and the cost of green hydrogen.
02 Technical advantages
There are two existing production paths for bio aviation kerosene:
Firstly, the hydrogenation refining method that obtains bio aviation kerosene by hydrogenation refining vegetable oil, gutter oil, or other high oil substances. This type of aviation kerosene has a similar carbon number distribution to conventional petroleum based aviation kerosene. Representative technologies include the next-generation renewable jet fuel technology of NESTEOIL in Finland and the renewable aviation fuel process of Honeywell UOP in the United States. The advantages of the hydrogenation refining method are mainly reflected in its mature technology, flexible product adjustment (which can flexibly adjust the production of green aviation kerosene and green diesel according to market demand), and strong adaptability to the market. However, the limitation of raw material sources (various oils and fats, seaweed, and shepherd's purse) is the biggest problem of the hydrogenation refining method, especially the competition between vegetable oil raw materials and humans for food and land. The other main source, gutter oil, has been continuously rising in price due to its scattered distribution, poor procurement channels, and insufficient supply. Currently, it has reached 6000-7000 yuan/ton, which has increased the cost of the final product, bio aviation kerosene, and also affected the widespread promotion and application of this technology.
Secondly, the Fischer Tropsch synthesis method that uses biomass such as cellulose and lignin as raw materials, first gasifies to generate syngas, which is then used to synthesize wax. The wax is then hydrocracked and hydroisomerized to produce bio aviation kerosene. Representative technologies include the first generation of bio aviation fuel and renewable diesel technology developed by Nesteoil in Finland, the iron-based catalytic high-temperature Fischer Tropsch synthesis process developed by Sasol in South Africa, and the inverse transformation+Fischer Tropsch synthesis process launched by Johnson Matthey in January 2022. The Fischer Tropsch synthesis method has a wide range of raw materials and significant carbon reduction effects, but the main components of the obtained liquid fuel are straight chain alkanes from C2 to C90. The C8 to C15 components that can truly be used as high-quality aviation kerosene only account for 25% of the synthesized product, and there are no cycloalkanes and aromatics, resulting in a low specific gravity and energy density of the obtained aviation kerosene, which means that the flight range of aircraft carrying the same volume of Fischer Tropsch synthesis fuel oil is short.
Compared to the above technologies, the entire process path of CO2AFTM technology at Tsinghua University is green. Specifically, there are four advantages: firstly, the obtained aviation kerosene components are concentrated in C9 to C11 aromatics, and the selectivity of high-quality aviation kerosene components exceeds 80%. By blending with straight chain alkanes, qualified aviation kerosene products can be obtained. Secondly, the selection of aromatic rings as the final product improved the thermodynamic efficiency of the reaction process, resulting in high energy utilization efficiency and significant energy-saving effects. Thirdly, by using acid-base heterojunction catalysts, the reaction can be carried out under mild conditions of 270~370 ℃ and above 2MPa, with lower overall energy consumption and cost. The fourth is that the source of raw materials is extensive and sustainable - this technology can produce synthetic gas from renewable energy sources such as biomass, and then produce aviation kerosene in a one-step process. It can also capture and purify carbon dioxide emissions from industrial enterprises, and produce aviation kerosene in a one-step process with hydrogen gas, thereby achieving dual carbon reduction and resource utilization. It is a truly green, low-carbon, and even negative carbon aviation kerosene production process.
03 Progress
A 100 ton/year trial has been completed, verifying the selectivity, stability, effectiveness, and safety of the catalyst, demonstrating the scientific, rational, and feasible nature of the entire process flow. From the results of the small-scale trial, it can be seen that the carbon dioxide hydrogenation technology for one-step production of green aviation kerosene consumes approximately 3.3 tons of carbon dioxide, 0.43 tons of hydrogen, and 0.5kg of catalyst for every 1 ton of aviation kerosene produced. Moreover, the catalyst has not significantly deactivated after continuous use for 3000 hours.
At present, the 10000 ton industrial testing device constructed using this technology is under construction and is expected to be put into trial operation in 2023. This industrial experimental device will mainly solve some problems that cannot be detected in small-scale tests during the engineering process of catalysts and process, but may affect the long-term operation of future industrial demonstration devices. After the industrial experiment is completed, a process package of 100000 to million tons can be formed based on the scale of green hydrogen, and industrial promotion and application can begin steadily.
The total investment for constructing a 300000 ton/year device using this technology is approximately 4.5 billion yuan. If using photovoltaic technology to produce green hydrogen, a 4.5Gw photovoltaic system (calculated at 1600 hours/year for photovoltaic power generation) and 180 sets of 1000 cubic meters/hour electrolytic water hydrogen production equipment are required.
04 Conclusion
This technology (CO2AFTM) uses CO2 and green hydrogen as raw materials and competes with world technology giants in the field (Green Jet FuelTM from Honeywell UOP in the United States and HyCOgenTM from Johnson Matthews in Europe). It proposes a Chinese solution in the world's low-carbon core technology field, which can fix carbon, create negative carbon emissions, help achieve net zero emissions in aviation flight, and convert wind and solar new energy electricity into liquid energy, contributing to China's carbon peak by 2030 The achievement of the carbon neutrality target by 2060 is of great significance.