Progress and Reflections on Biomass Conversion to Make SAF
From:
Zhonglin International Group Date:01-10 978 Belong to:Industry Related
With the continuous development of the global aviation industry, the demand for aviation kerosene is constantly increasing, and biomass energy, as the only natural carbon source in renewable energy, has broad development prospects because it can effectively replace fossil fuels. Currently, many countries have included the development of sustainable aviation fuels (SAF) in their aviation industry development strategies.
On June 28, 2022, China's first bio aviation coal industrial unit produced bio aviation coal for the first time at Sinopec Zhenhai Refining and Chemical Co., Ltd. The bio aviation coal industrial unit adopts production technology developed by Sinopec Petrochemical Science Research Institute. Using used cooking oil and edible oil, namely gutter oil, as raw materials to produce bio aviation coal.
The biggest difficulty in using gutter oil as a raw material to produce bio aviation coal is that gutter oil contains a large amount of fatty acid compounds, with an oxygen content of about 11%, while traditional raw materials such as petroleum have an oxygen content as low as 0.1%, with a difference of more than 100 times. Oxygen molecules directly affect the activity and stability of catalysts in refining equipment. In addition, gutter oil also contains various impurities such as sulfur, chlorine, and metal elements, which need to be removed one by one. For this purpose, the bio aviation coal industrial unit uses self-developed specialized catalysts and processes, and has been demonstrated and verified by industrial scale units.
In May 2022, Zhenhai Refining and Chemical Branch's HeFA route bio aviation coal products passed the Sustainable Biomaterials Roundtable (RSB) certification. This certification is the first global sustainability certification obtained by China's bio aviation coal products.
Sinopec stated that compared to traditional petroleum based aviation kerosene, bio aviation coal can reduce CO2 emissions by more than 50% throughout its entire lifecycle. The device has an annual design and processing capacity of 100000 tons, which can basically digest the gutter oil recovered from a city with a population of millions in a year. It can reduce CO2 emissions by about 80000 tons per year, which is equivalent to nearly 50000 economy cars being shut down for one year.
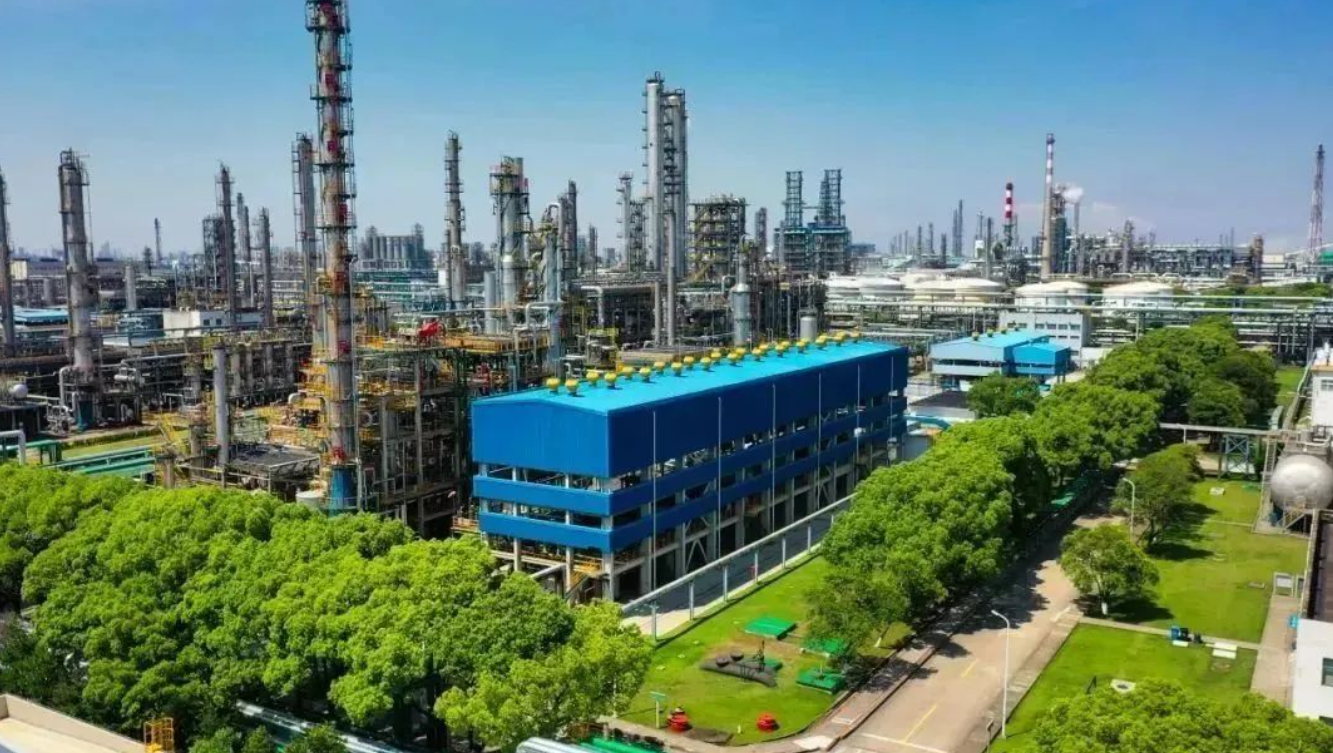
HEFA Route
HEFA (Ester and Fatty Acid of Hydrogenation) is a process of hydrogenation of triglycerides, saturated and unsaturated fatty acids in vegetable oil, food waste oil, and animal fat. The main product is biodiesel, and bio aviation coal accounts for about 15% of the total product. The aviation coal prepared by HEFA has advantages such as high thermal stability, good cold fluidity, high cetane number, and low exhaust emissions. However, low aromatic content may lead to low fuel lubricity and fuel leakage issues.
Due to borrowing from mature petrochemical processes, HEFA has lower technological barriers, shorter processes, controllable production costs, and is far lower than other technologies. Therefore, it has become the preferred technology route for enterprises in the context of increasing demand for sustainable aviation coal.
This process mainly adopts a two-stage process route:
1. Catalytic hydrogenation (pretreatment): By catalytic hydrogenation, unsaturated fatty acids and triglycerides are converted into saturated fatty acids. Triglycerides pass through β- Hydrogen elimination reaction generates fatty acids.
2. Hydrodeoxygenation and decarboxylation: Saturated fatty acids are converted into straight chain alkanes of C15-C18 through hydrogenation deoxygenation and decarboxylation reactions. In the early days, precious metal catalysts supported on zeolites or oxides were mainly used, but later transition metals such as Ni, Mo, Co or their supported bimetallic catalysts were gradually switched to.
3. Cracking and isomerization reactions: Further selective hydrocracking and deep isomerization of deoxygenated straight chain alkanes generate highly branched alkanes. Common catalysts include Pt loaded Al2O3, zeolite molecular sieves, etc. Finally, the mixed liquid fuel is separated into light gases, naphtha, and bio aviation coal through a distillation process.
The processes that use HEFA technology to produce aviation coal include the Ecofining process developed by UOP in the United States, the NExBTL process developed by Neste Oil in Finland, the Bio synfining process developed by Syntrol in the United States, the two-stage production process developed by the Energy and Environment Research Center in the United States, and the two-stage hydrogenation process developed by the China Petroleum and Chemical Science Research Institute.
At present, the supply of waste oils and fats has become the primary challenge for the development of the HEFA industry. Despite the rapid growth of sustainable aviation coal production capacity in China, there is a significant gap between actual production and planned production capacity due to the tight supply of raw materials. Taking Zhenhai Refining and Chemical as an example, large-scale production will be achieved in 2022. However, due to a shortage of kitchen waste oil, the annual output is only about 600 tons, far below the planned production capacity of 100000 tons.
GTJ Route
The technology of biomass gasification to produce bio aviation coal can promote the recycling of renewable resources and obtain high value-added green bio aviation coal, which is one of the important directions for achieving carbon reduction and carbon neutrality technology development in the aviation industry.
GTJ refers to the conversion of biogas, natural gas, or syngas into bio aviation coal. The main GTJ methods include Fischer Tropsch process (FT) and gas fermentation.
Fischer Tropsch synthesis (FT) technology is a process of producing liquid hydrocarbon fuels through synthesis gas. The production route of bio based Fischer Tropsch synthesis technology is basically consistent with the production route of bio aviation coal through coal processing. In 2009, the aviation coal technology for non petroleum based synthesis gas through Fischer Tropsch synthesis and hydrogenation conversion was recognized by ASTM7566. The FT-SPK products produced by this technology are also listed in Appendix 1 of ASTM D7566-15c, with a maximum blending ratio of 50% (volume fraction) for FT-SPK products.
The process of FT producing bio aviation coal can be divided into six steps: raw material pretreatment, biomass gasification, gas regulation, acid gas removal, FT synthesis, and crude oil refining.
Among them, the selection of catalysts has a significant impact on the types and properties of products. The catalysts that can be used include Fe, Ni, Co, and Ru, with Fe and Co commonly used in industry. High temperature FT and low temperature FT are two different reaction types. High temperature FT mainly produces gasoline, solvent oil, and olefins, while low temperature FT mainly produces kerosene, diesel, lubricating oil, and naphtha.
FT technology generates liquid fuels that typically do not contain sulfur or nitrogen and have high thermal stability through gasification and synthesis reactions of raw materials. In general, the conversion rate of FT synthesis is about 10% -15%. In terms of carbon emissions, the greenhouse gas emissions of sustainable aviation coal produced through FT synthesis are approximately 5.3-28.5 grams of carbon dioxide per megajoule, which is equivalent to achieving 67% -94% carbon reduction throughout the entire lifecycle of aviation fuel.
The raw materials used for preparing bio aviation coal contain a large amount of alkali metals such as Na and K, which are prone to accumulate on the catalyst during processing, causing structural damage and loss of activity, significantly reducing the service life of the catalyst. In addition, due to the relatively low aromatic content of bio aviation coal prepared by FT, the energy density is relatively low, so further improvement and optimization are needed in the production process.
At present, compared to HEFA, there is a temporary cost disadvantage in using FT technology to produce sustainable aviation coal. However, FT technology can fully leverage the advantages of abundant biomass resources in China's agricultural and forestry industries, and significantly increase the upper limit of sustainable aviation coal production capacity by utilizing raw materials such as straw; On the other hand, China's FT technology is relatively mature, relying on the industrial foundation of coal to oil technology. The original Fischer Tropsch synthesis unit can quickly transform and produce biomass fuel at a lower cost.
Repost from: https://mp.weixin.qq.com/s/qZbHr9tXgLRmzu11Wpq6Qw
Author: Xu Run, Director of the Coal and Syngas Conversion Research Office of Sinopec Institute of Petroleum Sciences
On June 28, 2022, China's first bio aviation coal industrial unit produced bio aviation coal for the first time at Sinopec Zhenhai Refining and Chemical Co., Ltd. The bio aviation coal industrial unit adopts production technology developed by Sinopec Petrochemical Science Research Institute. Using used cooking oil and edible oil, namely gutter oil, as raw materials to produce bio aviation coal.
The biggest difficulty in using gutter oil as a raw material to produce bio aviation coal is that gutter oil contains a large amount of fatty acid compounds, with an oxygen content of about 11%, while traditional raw materials such as petroleum have an oxygen content as low as 0.1%, with a difference of more than 100 times. Oxygen molecules directly affect the activity and stability of catalysts in refining equipment. In addition, gutter oil also contains various impurities such as sulfur, chlorine, and metal elements, which need to be removed one by one. For this purpose, the bio aviation coal industrial unit uses self-developed specialized catalysts and processes, and has been demonstrated and verified by industrial scale units.
In May 2022, Zhenhai Refining and Chemical Branch's HeFA route bio aviation coal products passed the Sustainable Biomaterials Roundtable (RSB) certification. This certification is the first global sustainability certification obtained by China's bio aviation coal products.
Sinopec stated that compared to traditional petroleum based aviation kerosene, bio aviation coal can reduce CO2 emissions by more than 50% throughout its entire lifecycle. The device has an annual design and processing capacity of 100000 tons, which can basically digest the gutter oil recovered from a city with a population of millions in a year. It can reduce CO2 emissions by about 80000 tons per year, which is equivalent to nearly 50000 economy cars being shut down for one year.
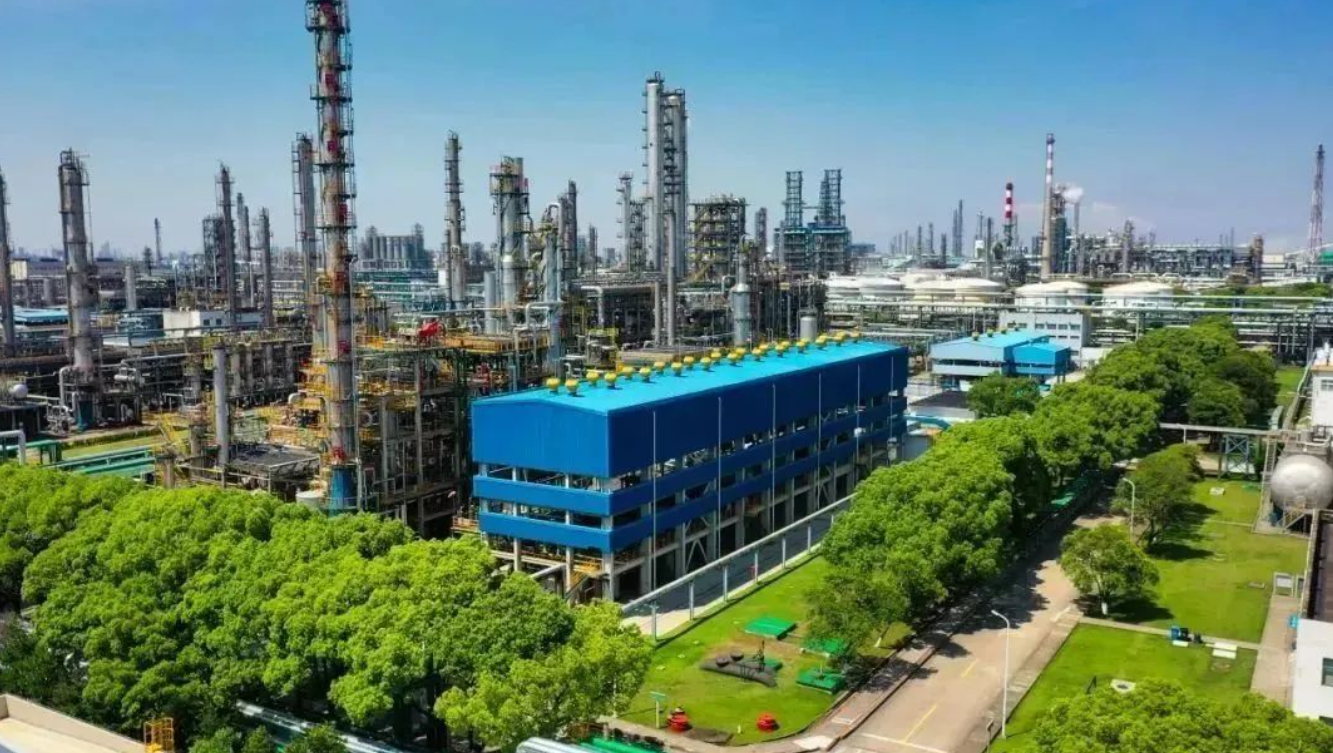
HEFA Route
HEFA (Ester and Fatty Acid of Hydrogenation) is a process of hydrogenation of triglycerides, saturated and unsaturated fatty acids in vegetable oil, food waste oil, and animal fat. The main product is biodiesel, and bio aviation coal accounts for about 15% of the total product. The aviation coal prepared by HEFA has advantages such as high thermal stability, good cold fluidity, high cetane number, and low exhaust emissions. However, low aromatic content may lead to low fuel lubricity and fuel leakage issues.
Due to borrowing from mature petrochemical processes, HEFA has lower technological barriers, shorter processes, controllable production costs, and is far lower than other technologies. Therefore, it has become the preferred technology route for enterprises in the context of increasing demand for sustainable aviation coal.
This process mainly adopts a two-stage process route:
1. Catalytic hydrogenation (pretreatment): By catalytic hydrogenation, unsaturated fatty acids and triglycerides are converted into saturated fatty acids. Triglycerides pass through β- Hydrogen elimination reaction generates fatty acids.
2. Hydrodeoxygenation and decarboxylation: Saturated fatty acids are converted into straight chain alkanes of C15-C18 through hydrogenation deoxygenation and decarboxylation reactions. In the early days, precious metal catalysts supported on zeolites or oxides were mainly used, but later transition metals such as Ni, Mo, Co or their supported bimetallic catalysts were gradually switched to.
3. Cracking and isomerization reactions: Further selective hydrocracking and deep isomerization of deoxygenated straight chain alkanes generate highly branched alkanes. Common catalysts include Pt loaded Al2O3, zeolite molecular sieves, etc. Finally, the mixed liquid fuel is separated into light gases, naphtha, and bio aviation coal through a distillation process.
The processes that use HEFA technology to produce aviation coal include the Ecofining process developed by UOP in the United States, the NExBTL process developed by Neste Oil in Finland, the Bio synfining process developed by Syntrol in the United States, the two-stage production process developed by the Energy and Environment Research Center in the United States, and the two-stage hydrogenation process developed by the China Petroleum and Chemical Science Research Institute.
At present, the supply of waste oils and fats has become the primary challenge for the development of the HEFA industry. Despite the rapid growth of sustainable aviation coal production capacity in China, there is a significant gap between actual production and planned production capacity due to the tight supply of raw materials. Taking Zhenhai Refining and Chemical as an example, large-scale production will be achieved in 2022. However, due to a shortage of kitchen waste oil, the annual output is only about 600 tons, far below the planned production capacity of 100000 tons.
GTJ Route
The technology of biomass gasification to produce bio aviation coal can promote the recycling of renewable resources and obtain high value-added green bio aviation coal, which is one of the important directions for achieving carbon reduction and carbon neutrality technology development in the aviation industry.
GTJ refers to the conversion of biogas, natural gas, or syngas into bio aviation coal. The main GTJ methods include Fischer Tropsch process (FT) and gas fermentation.
Fischer Tropsch synthesis (FT) technology is a process of producing liquid hydrocarbon fuels through synthesis gas. The production route of bio based Fischer Tropsch synthesis technology is basically consistent with the production route of bio aviation coal through coal processing. In 2009, the aviation coal technology for non petroleum based synthesis gas through Fischer Tropsch synthesis and hydrogenation conversion was recognized by ASTM7566. The FT-SPK products produced by this technology are also listed in Appendix 1 of ASTM D7566-15c, with a maximum blending ratio of 50% (volume fraction) for FT-SPK products.
The process of FT producing bio aviation coal can be divided into six steps: raw material pretreatment, biomass gasification, gas regulation, acid gas removal, FT synthesis, and crude oil refining.
Among them, the selection of catalysts has a significant impact on the types and properties of products. The catalysts that can be used include Fe, Ni, Co, and Ru, with Fe and Co commonly used in industry. High temperature FT and low temperature FT are two different reaction types. High temperature FT mainly produces gasoline, solvent oil, and olefins, while low temperature FT mainly produces kerosene, diesel, lubricating oil, and naphtha.
FT technology generates liquid fuels that typically do not contain sulfur or nitrogen and have high thermal stability through gasification and synthesis reactions of raw materials. In general, the conversion rate of FT synthesis is about 10% -15%. In terms of carbon emissions, the greenhouse gas emissions of sustainable aviation coal produced through FT synthesis are approximately 5.3-28.5 grams of carbon dioxide per megajoule, which is equivalent to achieving 67% -94% carbon reduction throughout the entire lifecycle of aviation fuel.
The raw materials used for preparing bio aviation coal contain a large amount of alkali metals such as Na and K, which are prone to accumulate on the catalyst during processing, causing structural damage and loss of activity, significantly reducing the service life of the catalyst. In addition, due to the relatively low aromatic content of bio aviation coal prepared by FT, the energy density is relatively low, so further improvement and optimization are needed in the production process.
At present, compared to HEFA, there is a temporary cost disadvantage in using FT technology to produce sustainable aviation coal. However, FT technology can fully leverage the advantages of abundant biomass resources in China's agricultural and forestry industries, and significantly increase the upper limit of sustainable aviation coal production capacity by utilizing raw materials such as straw; On the other hand, China's FT technology is relatively mature, relying on the industrial foundation of coal to oil technology. The original Fischer Tropsch synthesis unit can quickly transform and produce biomass fuel at a lower cost.
Repost from: https://mp.weixin.qq.com/s/qZbHr9tXgLRmzu11Wpq6Qw
Author: Xu Run, Director of the Coal and Syngas Conversion Research Office of Sinopec Institute of Petroleum Sciences